In coding and marking, Industry 4.0 technologies have been increasingly adopted to enhance efficiency, accuracy, and integration with broader manufacturing processes. Coding and marking are critical in manufacturing for product identification, traceability, regulatory compliance, and to provide consumers with essential product information. With Industry 4.0, the integration of smart technologies in coding and marking systems brings several significant advancements.
What is Industry 4.0?
Industry 4.0, also known as the Fourth Industrial Revolution, refers to the current trend of automation and data exchange in manufacturing technologies. It encompasses various concepts, including cyber-physical systems, the Internet of Things (IoT), cloud computing, and cognitive computing.
Why is Industry 4.0 important for the manufacturing industry?
Industry 4.0 integrates physical production and operations with smart digital technology, machine learning, and big data to create a more holistic and better-connected ecosystem for companies focusing on manufacturing and supply chain management.
The core idea behind Industry 4.0 is to make manufacturing more efficient, flexible, and customizable through the use of smart technologies. It enables factories to be more responsive to the needs of customers, reduce operational costs, improve production efficiency, and increase the quality of products.
The MapleJet Hx industrial inkjet printers are designed with features that perfectly align with the principles of Industry 4.0, emphasizing enhanced connectivity, automation, and intelligent data utilization.
Embracing Industry 4.0: MapleJet Hx Advanced Features
Numerous coding and marking technologies, including thermal inkjet printers known for their exceptional coding quality, remain grounded in traditional operational processes. However, these coding solutions often lack Industry 4.0 features like cloud integration and real-time analytics. This gap hinders their adaptability and efficiency in the digital-driven manufacturing landscape, where seamless system integration and data-driven operations are key to optimizing production and enhancing transparency.
How does MapleJet secure a spot in the Industry 4.0 arena?
- Seamless Connectivity with Wi-Fi. MapleJet Hx printer advances beyond traditional Thermal Inkjet (TIJ) systems, which typically depend on a single, directly connected Human-Machine Interface (HMI). Utilizing Wi-Fi, MapleJet enables devices like smartphones, tablets, or computers to connect to one or several printers on the production line, offering flexibility and enhanced oversight. This is achieved through a built-in Wi-Fi module or an access point for internet connectivity, allowing seamless management of printing operations directly from the user’s device. This approach not only facilitates greater operational mobility but also supports more efficient monitoring and control over the printing process, marking a significant leap in coding and marking technology adaptability.
2. AutoPilot for Easy Third-Party Integration. The Hx printers come equipped with a special AutoPilot feature, designed to enhance control and monitoring capabilities via third-party systems. This innovative function allows a PC or PLC—running dedicated software—to send commands to the Hx printer through various connection options such as Wi-Fi, RS232, or USB ports. In response, the printer communicates back, ensuring a two-way interaction for streamlined operations. This interoperability not only simplifies the integration into existing systems but also offers flexibility in how the printers are managed within different manufacturing environments, reinforcing the smart, connected ethos of Industry 4.0.
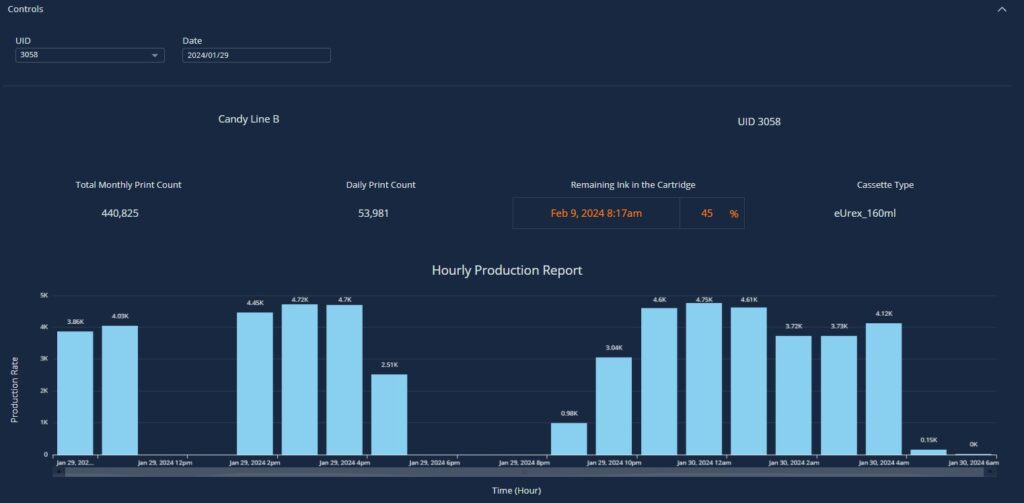
3. MapleJet Cloud for Production Insights. The MapleJet Cloud service is an integral feature that significantly enhances productivity by providing insightful production analysis and facilitating planned maintenance. With real-time information accessible through the cloud, customers can preemptively identify and address printer issues, preventing costly downtime and potential manufacturing interruptions that could impact production throughput and line availability.
Case Studies and Applications
The adoption of a cloud-based Hx Nitro printer by a multinational company in Pakistan exemplifies the practical application of Industry 4.0 technologies in enhancing operational efficiency and data management. Cloud connectivity enables real-time data access, ensuring that production adjustments can be made swiftly to meet demand, improve productivity, and reduce downtime.
For distributors and agents, the integration of cloud technology with devices like the Hx Nitro printer presents a significant opportunity for enhancing service and maintenance operations. Through cloud connectivity, they can access real-time diagnostics and performance data from the printers they manage, enabling proactive maintenance and swift troubleshooting. This capability ensures that potential issues can be identified and addressed before they escalate into major problems, reducing downtime and maintaining operational efficiency. Moreover, the cloud facilitates remote updates and adjustments, allowing distributors and agents to offer timely support and optimize printer performance without the need for on-site visits. This not only improves service quality but also enhances the overall value proposition for customers, leveraging the cloud to create a more responsive and efficient maintenance ecosystem.
Recent Comments